Impressão 3D em metal diminui custo de fabricação de peça automotiva em 17%
A fabricante tcheca de ferramentas Innomia desenvolve os processos de manufatura para a fabricação de peças plásticas moldadas por injeção para a Magna, empresa de engenharia e distribuição de componentes automotivos. Em dada altura do processo, quando da manufatura de um componente dianteiro central de um carro da marca Škoda, revelou-se uma enorme dificuldade em se otimizar o molde usado no processo de moldagem por injeção. O molde é usado para fabricar o componente a partir de uma fibra de vidro reforçada com material plástico que requer que o calor do molde se dissipe uniformemente, a fim de minimizar a distorção e manter a qualidade da peça utilizada nos carros da Škoda. Infelizmente, a ferramenta usada para dar forma à peça moldada por injeção é feita com uma liga de berilio-cobre, que possui alta condutividade térmica, mas apenas de um lado.
O problema
Isso fazia com que a distribuição da temperatura fosse muito desigual e resultaria em um maior número de peças imperfeitas ou deformadas. Além disso, o molde simplesmente não arrefecia rapidamente o suficiente para maximizar a saída de calor. Quanto mais rápido o calor é removido do molde, mais rapidamente a peça pode ser ejetada para que a próxima parte seja injetada; mas, na verdade, o que ocorria era que se levava mais tempo que o desejável no período de resfriamento, atrasando ordens de serviço e aumentando os custos de produção.
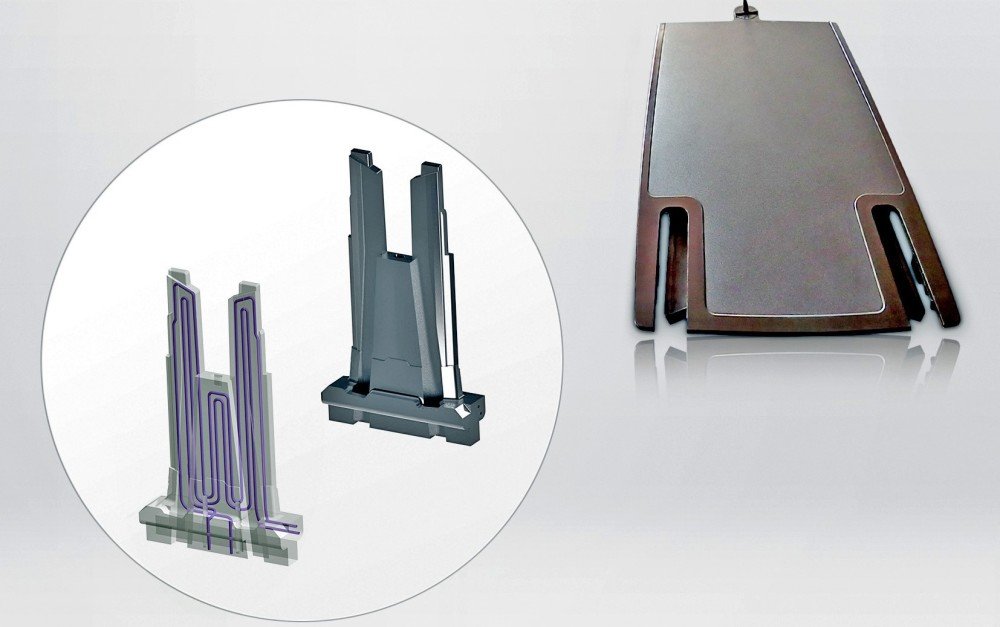
O molde também necessitava de refrigeração por água para dissipar o calor, no entanto, como o diferencial de temperatura era muito alto, o resultado era um elevado nível de umidade que acelerava a corrosão da peça. Isso exigia que a peça fosse limpa a cada duas semanas, um processo bastante demorado e intensivo.
A solução
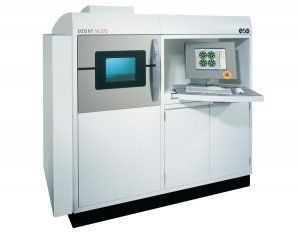
Quando a Innomia começou a tratar dos problemas que a Magna possuía com seus sistemas de ferramentas, a primeira prioridade foi o desenvolvimento de uma nova ferramenta com um sistema de refrigeração otimizado para a remoção de calor. A empresa decidiu usar a impressão 3D para solucionar o problema, valendo-se de uma impressora 3D de sinterização de metal a laser — Direct Metal Laser Sintering (DMLS) — da EOS, capaz de fabricar componentes com praticamente qualquer geometria externa e interna. A equipe da Innomia desenhou a solução criando um sistema integrado de canais de refrigeração de apenas 3 mm de largura. A peça foi impressa em 3D em uma EOSINT M 270 tendo como insumo um material de pó de aço maraging, um metal de baixo carbono conhecido pela sua força excepcional sem perder a maleabilidade.
O resultado
Além da nova peça, mais durável, a Innomia também foi capaz de endurecer a parte final usando um tratamento pós impressão que resultou em um elevado nível de resistência ao desgaste e custos de manutenção muito mais baixos. Os novos canais de arrefecimento na ferramenta, agora uniformes, resultaram em um aumento de 17% na produtividade e na velocidade do ciclo de produção. Além disso, como a questão da deformação da peça já não é mais um problema, a equipe de produção pode se concentrar na qualidade e reprodução do componente.
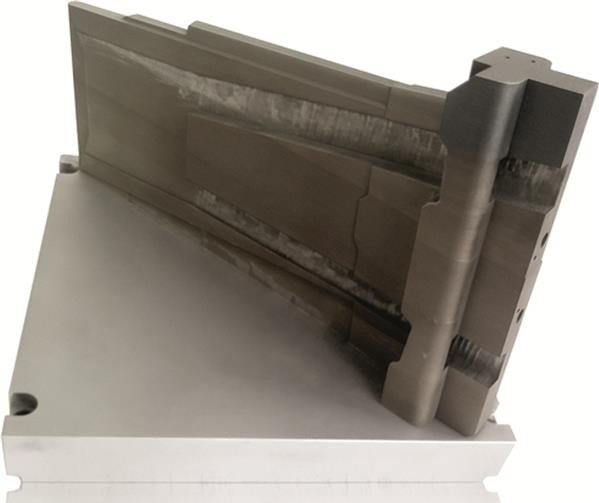
Graças à tecnologia de impressão 3D em metal, não só diminuiu-se a complexidade da produção do componente para um nível superior de qualidade, como todo o processo tornou-se mais rápido, mais barato e mais eficiente. O resultado final da nova ferramenta impressa em 3D foi uma economia de € 20.000 após a fabricação de 370.000 peças.
Fonte: 3D Printing Industry
Pingback: Metal 3D Printing Discussion Will Highlight in São Paulo — A Few Questions For: EOS – 3DPrint.com
Pingback: Metal 3D Printing Discussion Will Highlight in São Paulo — A Few Questions For: EOS – 3DPrint.com
Como faço para saber o custo de uma peça em metal em formato de \”U\” com dimensões de 30 x 30 centímetros
Você pode tirar essa e mais dúvidas pelo grupo “Impressora 3D Brasil” no Facebook. Segue o link: https://www.facebook.com/groups/impressora3d/
Abraço,
Laura
Como faço para saber o custo de uma peça em metal em formato de \”U\” com dimensões de 30 x 30 centímetros
Você pode tirar essa e mais dúvidas pelo grupo “Impressora 3D Brasil” no Facebook. Segue o link: https://www.facebook.com/groups/impressora3d/
Abraço,
Laura
como posso fabricar meu molde com as cavidades em 3d, incluindo as gavetas?
como posso fabricar meu molde com as cavidades em 3d, incluindo as gavetas?